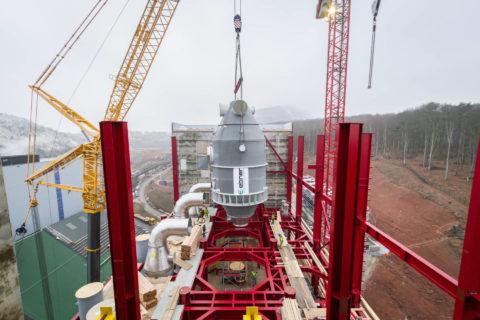
Large-Scale Plant for the Production of Potassium Chloride (MOP) from Clarified Hot Solution
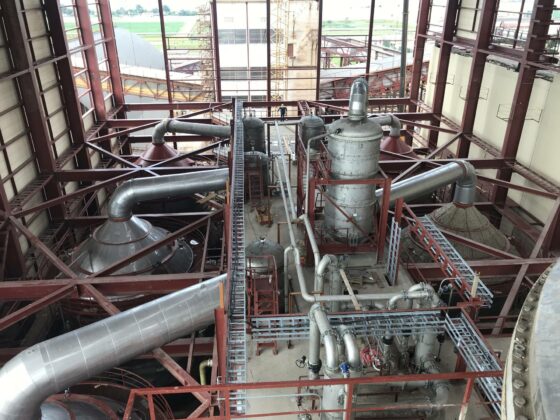
EBNER, in collaboration with partners, was awarded the contract for the planning, delivery, and erection of a multi-effect plant for the vacuum cooling crystallization of potassium chloride from clarified hot solution by the largest potash producer in Belarus before the year 2020.
- Region: Belarus
- Plant Type/ Process: Vacuum Cooling Crystallization
- Services: Engineering, Manufacturing, Erection Supervision, Commissioning Supervision
Strategic Expansion: EBNER Designs Plant for Potassium Chloride Processing
The plant designed by EBNER aims to expand the client’s production capacity and replace an older existing facility. Generally, potassium chloride, extracted through mining, can be transformed into marketable fertilizer through two core processes:
- Vacuum Cooling Crystallization
- Flotation
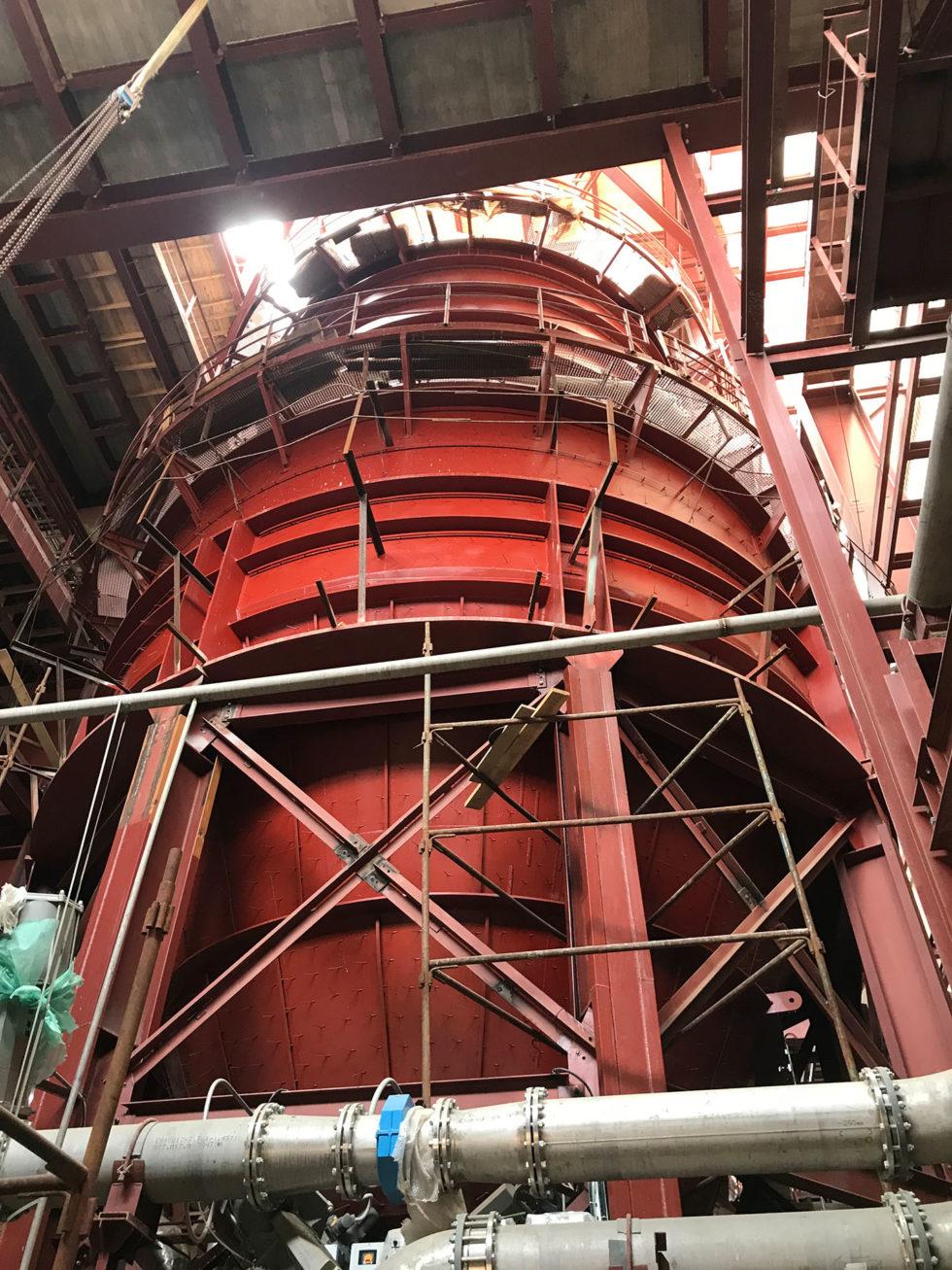
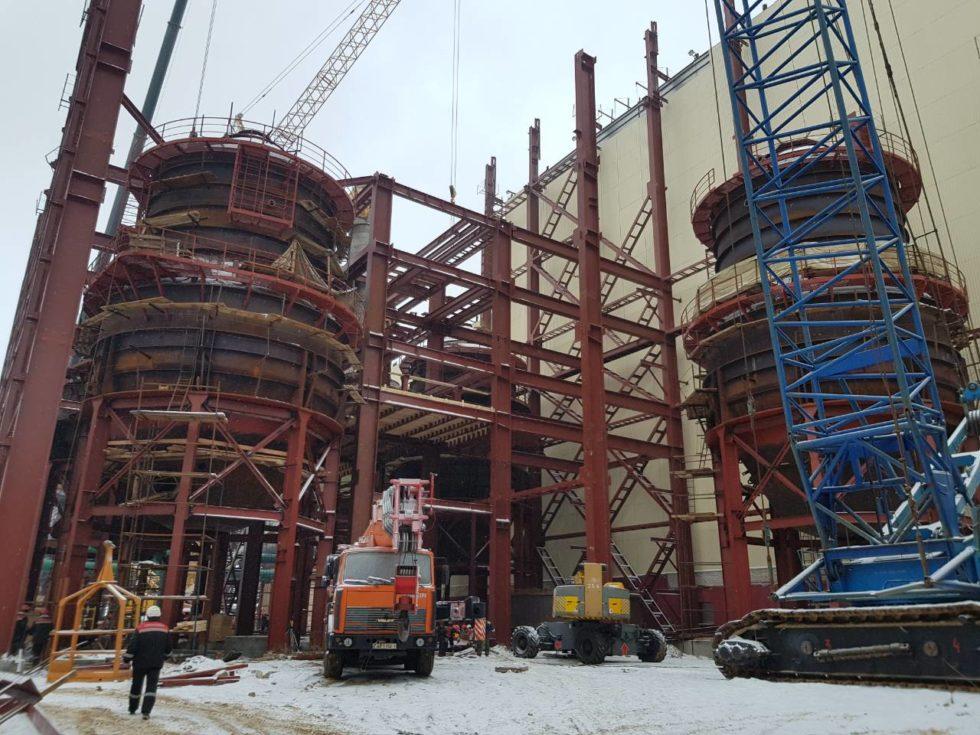
Integrated Fertilizer Production: Insight into the Vacuum Cooling Crystallization Process
The plant operates on the principle of vacuum cooling crystallization and integrates into the typical production flow for potassium chloride fertilizer as follows:
- Mining of raw ore
- Hot clarification: Dissolving KCl and NaCl salts in raw ore and separating insoluble components
- Vacuum cooling crystallization: Cooling the solution, causing KCl to precipitate while keeping NaCl in solution with the addition of water
- Salt separation or post-treatment: Separating solution and, for example, compacting/granulating the KCl salt
The hot solution is introduced into the plant at about 90-100°C. At each stage of the plant, vacuum is applied to evaporate water from the incoming solution. This process extracts heat from the solution, cooling it down. As the solubility of KCl decreases with lowering temperature, the solubility is exceeded, and salt crystallizes. The resulting suspension is then transferred to the next stage and cooled again using the same process. This leads to the growth of previously formed crystals. By repeating this process, the solution is eventually cooled to about 30°C and sent for salt separation or post-treatment.
The separated brine in salt separation is returned to the hot clarification process to dissolve new salt. To achieve the temperature in hot clarification, the solution is used to condense as much of the vapor generated in the vacuum cooling crystallization as possible. This maximizes heat recovery. The remaining heating is done using fresh steam.
The production facility is of great importance to the client, as it represents the core of production. EBNER and its partners were awarded this contract mainly due to their good reputation, customer proximity, and the highly efficient heat recovery of the vacuum cooling crystallization plant.
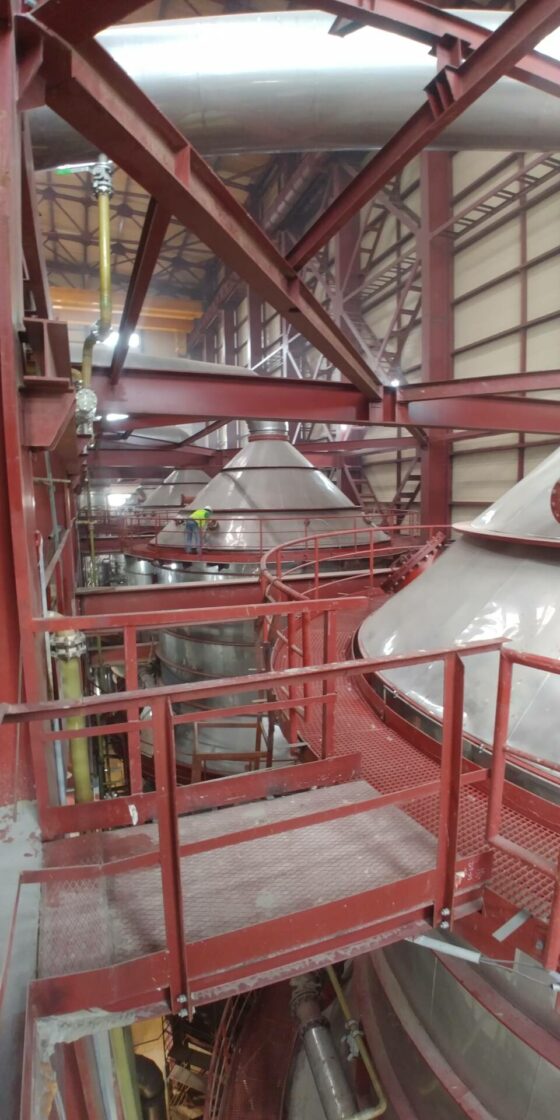
Technical Data of the Plant
- Feed rate of solution: 1,700 m³/h
- Main components of the solution: KCl, NaCl
- Water evaporation: 155 t/h
- Product: KCl
- Production volume: 195 t/h
Scope of Supply
EBNER’s scope of supply included, among others:
- Basic and detail engineering incl. partial design of main components
- Prefabrication of main components for completion on-site
- Erection supervision for main components of the entire plant
- Commissioning supervision of the entire plant
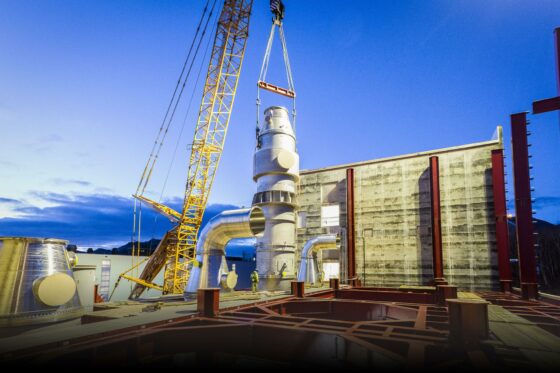
EBNER – your competent partner in plant engineering
Due to many years of experience in a wide variety of industries and with a wide variety of solutions, EBNER is your contact to optimally carry out the process design, planning, delivery and assembly according to your needs.
Other References
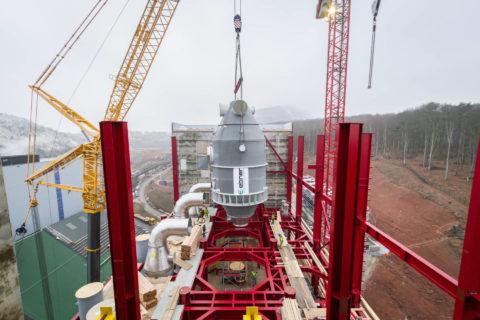
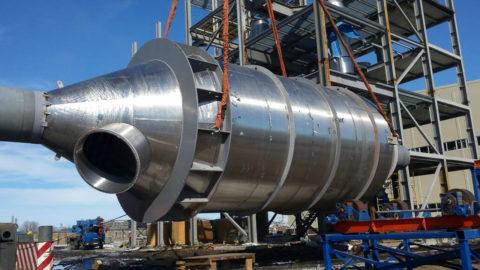
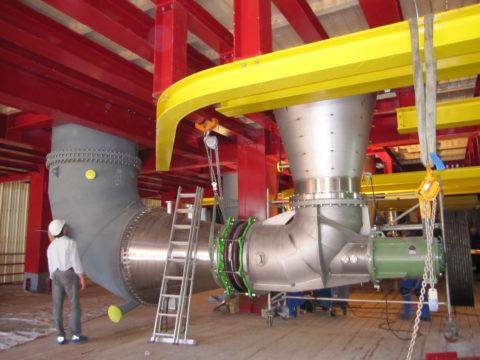
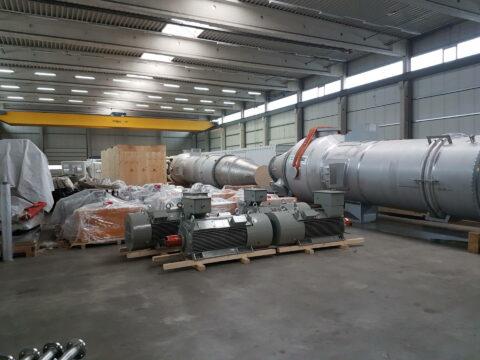
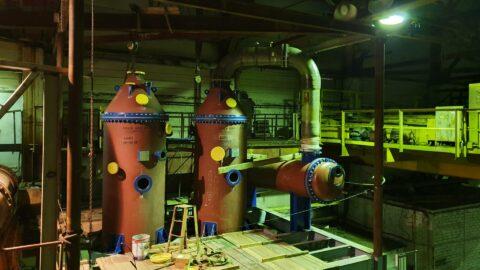
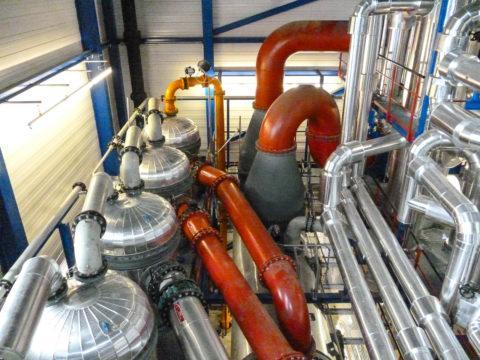
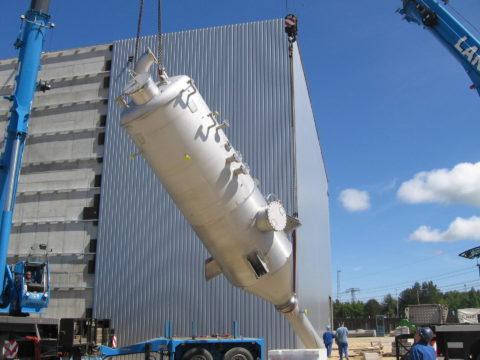
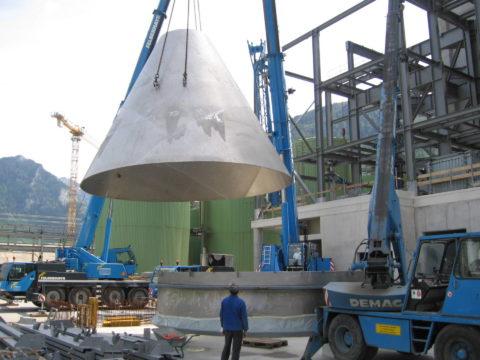

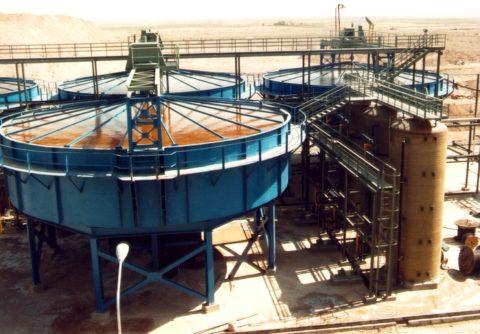
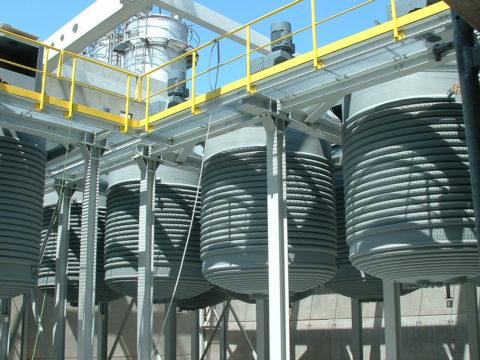
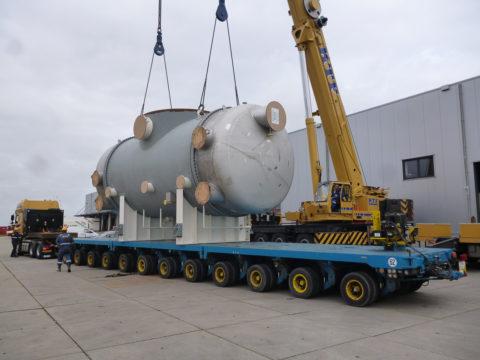