
Crystallization of KCl (MOP)
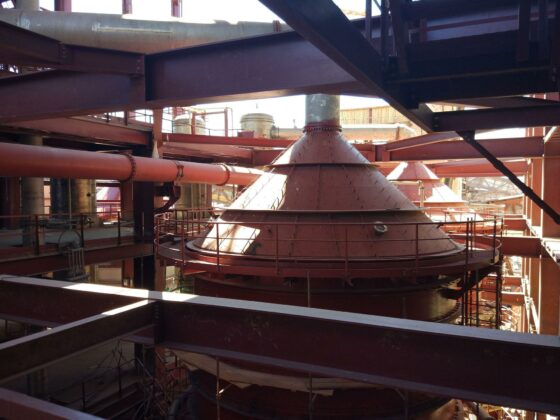
Crystallization plants for KCl involve cooling crystallization in almost all cases. This utilizes the significantly decreasing solubility of potassium chloride with lowering temperature to cool the saturated potassium chloride solution and crystallize KCl.
Typically, a hot, KCl-saturated solution is produced either through conventional mining or solution mining. Usual temperatures are around 95°C. This solution is saturated not only with KCl but also with accompanying salts such as magnesium and calcium salts, and particularly with NaCl, which is enriched in the dissolution of the raw salt in the so-called hot dissolving process or through solution mining underground.
After any preliminary treatment, the solution is led into a vacuum cooling crystallization plant. Here, by lowering the pressure, water is evaporated, which lowers the temperature of the solution.
The evaporated water is usually reintroduced into the process. This ensures that the potassium chloride crystallizes, and the crystallization of sodium chloride is largely suppressed. Sodium chloride should only be present in small amounts, depending on the desired quality of the MOP fertilizer (Muriate of Potash), between 2 and 5% in the salt.
The plant is brought to the final temperature in several stages.
Usually, the final temperature is determined by the cooling water temperature available at the plant. Typically, the final temperature varies with the cooling water, usually around 35°C.
The resulting suspension from the last stage is put into a salt separation unit. Here, the crystallized salts are separated from the solution.
After salt separation, the solution is reheated for hot dissolving or underground to dissolve the raw salt and then reintroduced into the cycle of the vacuum cooling crystallization plant.
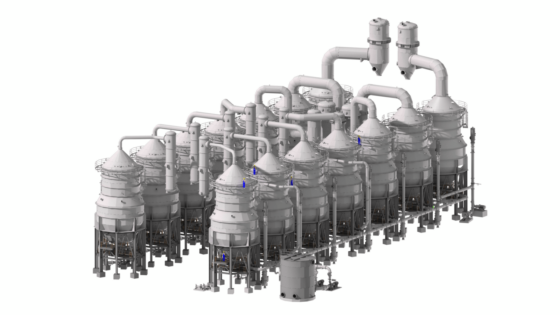
To minimize the primary energy costs for heating this solution, it is typically pumped through easy-to-clean tube bundle heat exchangers connected to the individual stages of the vacuum cooling crystallization plant – thus recovering the heat from each stage and reintroducing it into the overall cycle.
The final reheating before the respective dissolving is usually done with fresh steam.
Occasionally, crystallization plants for KCl are also carried out through direct cooling. However, these plants are mainly used to remove small amounts of potassium chloride from process solutions or to cool further than the cooling water temperature allows, for example, by refrigerants.
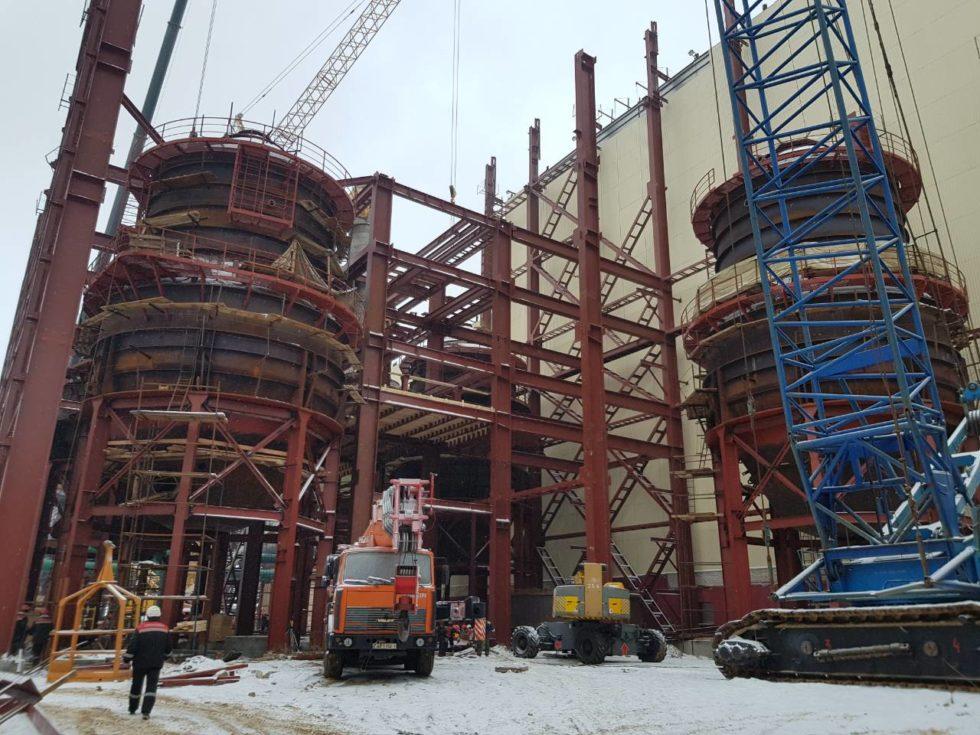
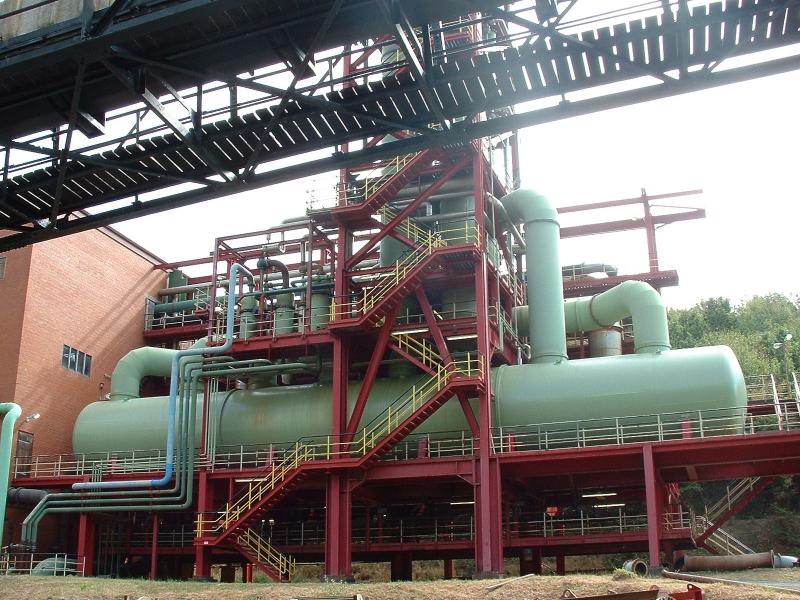
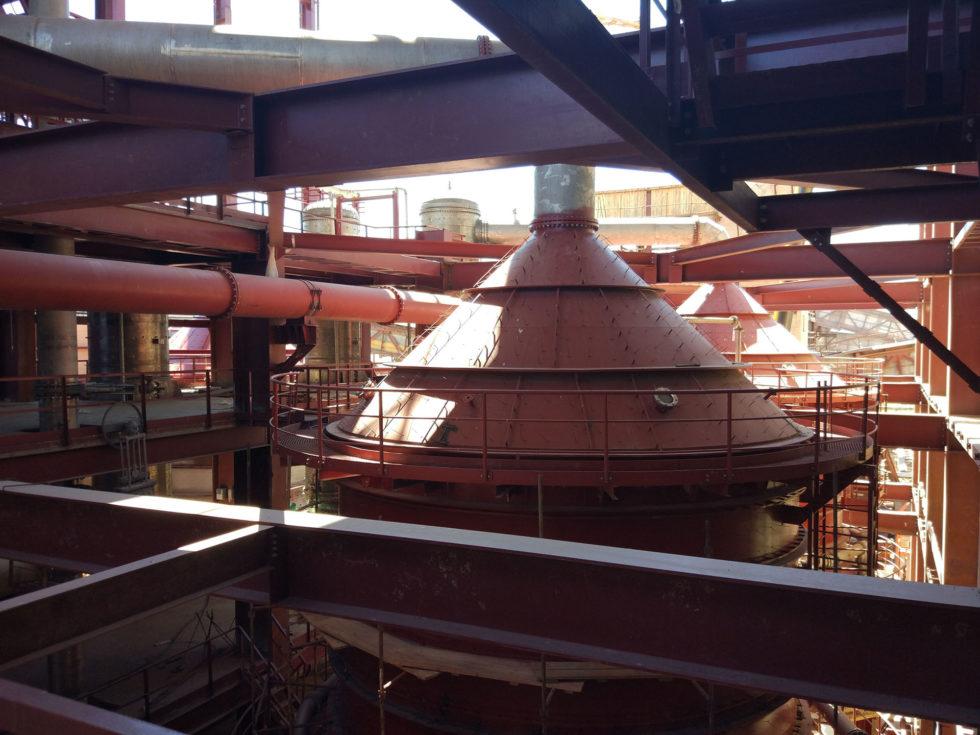
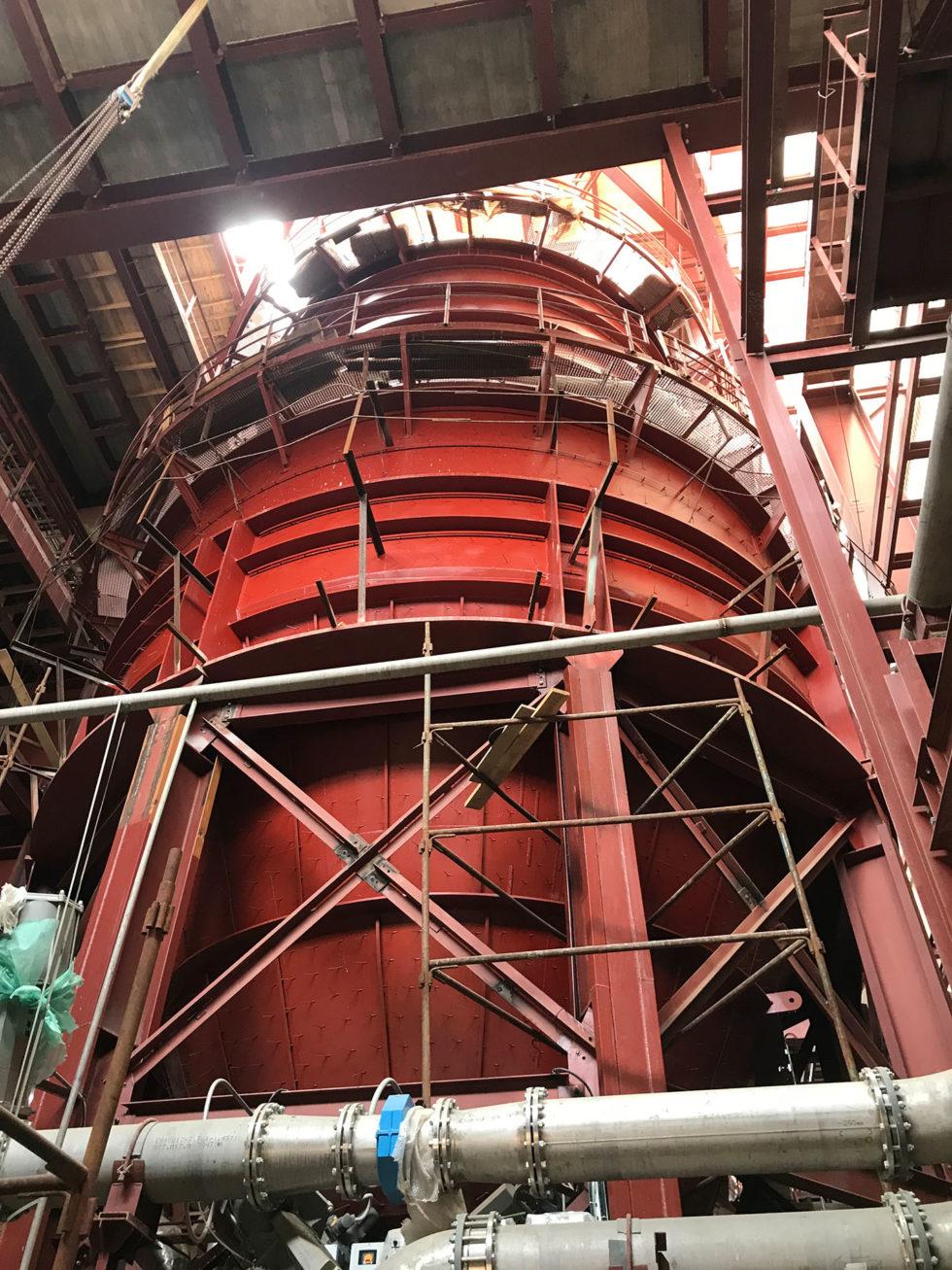
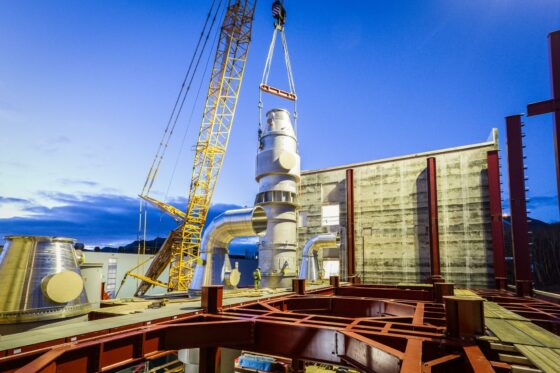
EBNER – your competent partner in plant engineering
Thanks to many years of experience in various industries and with different solutions, EBNER is your contact for optimally executing the process design, planning, delivery, and erection according to your needs.
Frequently Asked Questions
How is it ensured that the produced KCl meets the specific purities for MOP fertilizers?
To maintain the quality of the resulting potassium chloride within the usual market values for MOP, various measures are carried out. To crystallize further salts only within the usual market proportions, water is added to the solution during cooling.
How is the necessary crystal size for MOP fertilizers achieved?
To keep the crystal size of the potassium chloride within the usual range, the plant is designed to handle the KCl gently.
To keep the proportion of fine grains as low as possible, the crystal concentration in the individual stages can be adjusted in standing crystallizers.
The sizes of the apparatus are also selected so that there is enough residence time for crystal growth.
What design is chosen for the crystallizers?
The crystallizers are usually designed as DTB (Draft Tube Baffle) crystallizers.
Alternatively, the plant can also be executed with horizontal crystallizers.
Other Applications

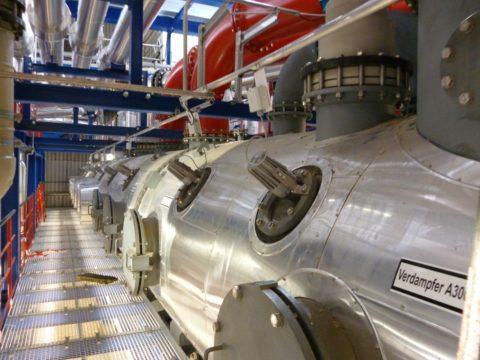
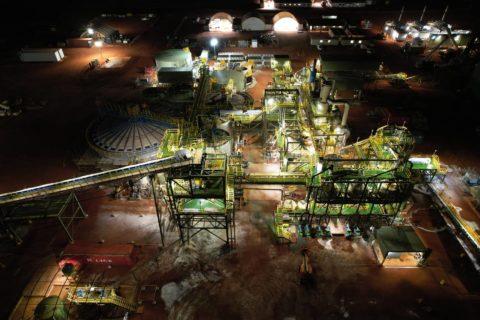
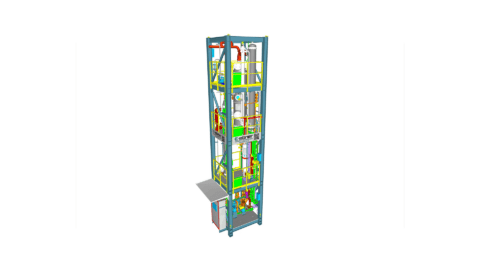
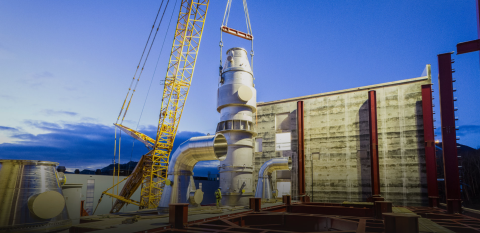
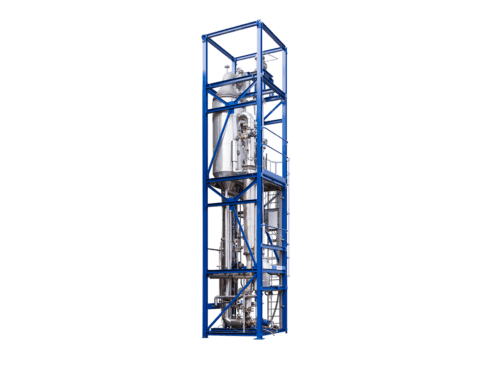
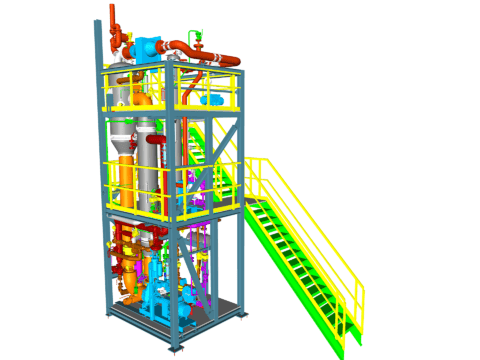
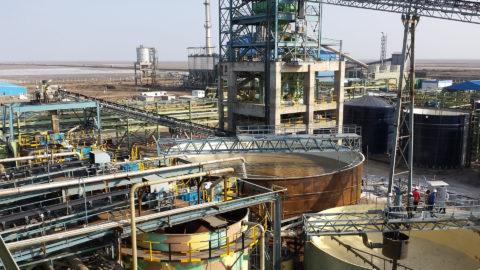
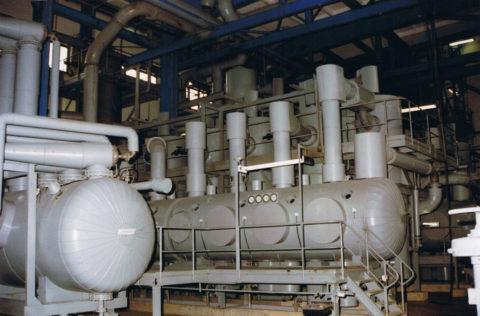
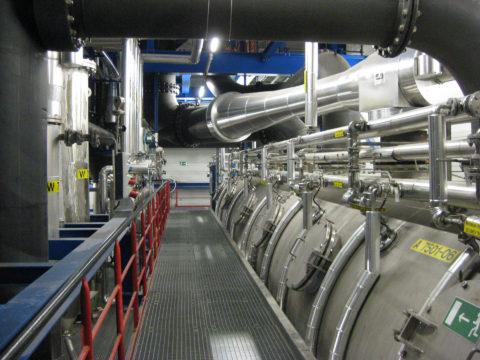
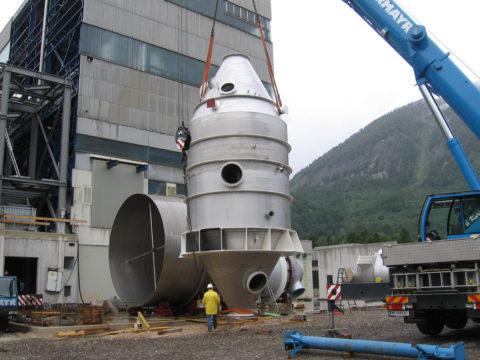
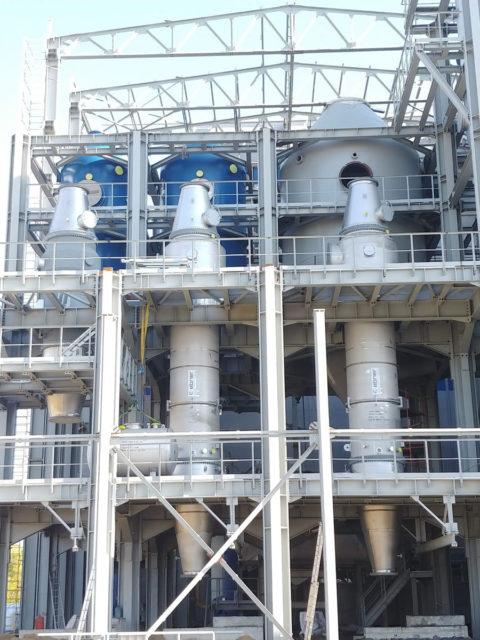
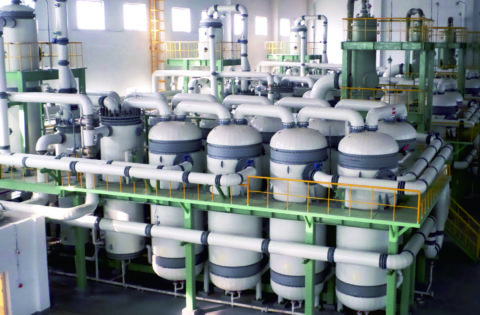
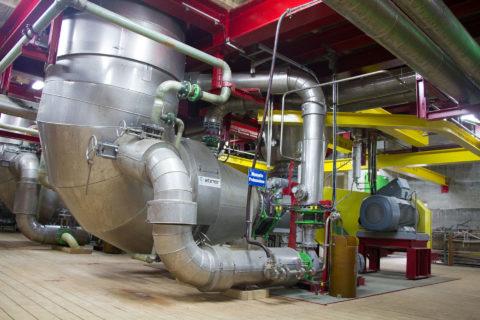
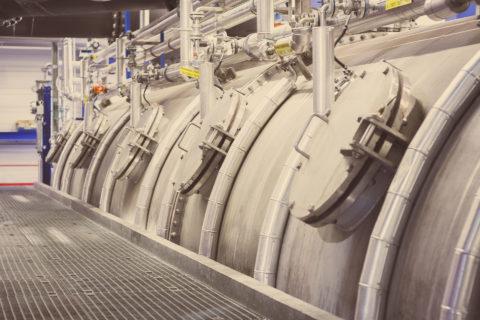