
Evaporation of Spin Bath & Crystallization of Sodium Sulfate
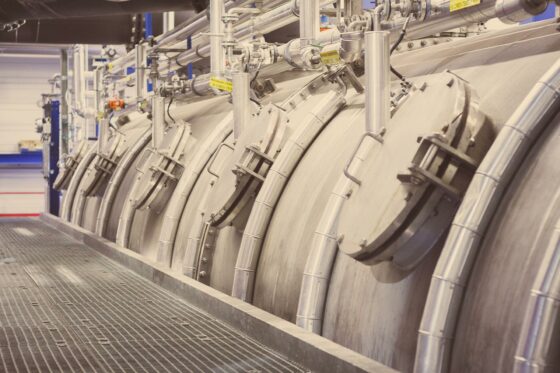
In the production of viscose fibers, the spin bath is diluted with water and enriched with sodium sulfate. To regenerate the spin bath and make it reusable for the overall process, both components must be removed from the plant. Typically, 3 sub-plants are used for this purpose.
These are:
- For water removal, evaporation from the solution in the flash evaporation plant.
- To reduce the sodium sulfate load, vacuum cooling crystallization of the solution to produce Glauber’s salt (Na₂SO₄ 10H₂O).
- Calcination to convert Glauber’s salt (Na₂SO₄ 10H₂O) into anhydrous sodium sulfate (Na₂SO₄).

First Sub-plant: Evaporation of the Solution in a Flash Evaporation Plant
In flash evaporation, the solution to be evaporated is fed into a horizontal evaporator.
This evaporator consists of several chambers through which the solution flows, being relaxed from stage to stage by increasingly lower pressure, thus evaporating water. This cools the solution.
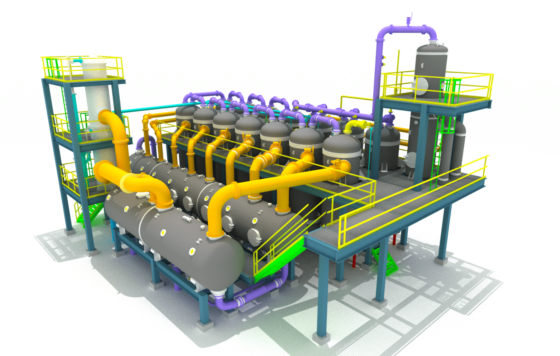
The concentrated solution then leaves the evaporation plant into one of the colder stages, depending on the desired final temperature. The rest of the solution continues to the coldest stage and is then pumped through several surface condensers with the help of a circulation pump, where most of the vapor generated during the flash evaporation in the individual stages is condensed.
This warms the solution again and recovers the generated flash energy.
In the final heating with fresh steam or steam from other parts of the overall process (e.g., from the calcination plant), the solution is reheated and then flows into the first flash stage.
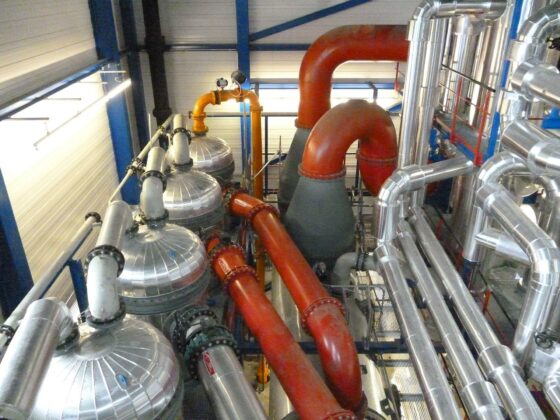
Second Sub-plant: Vacuum Cooling Crystallization of Glauber’s Salt (Na₂SO₄ 10H₂O)
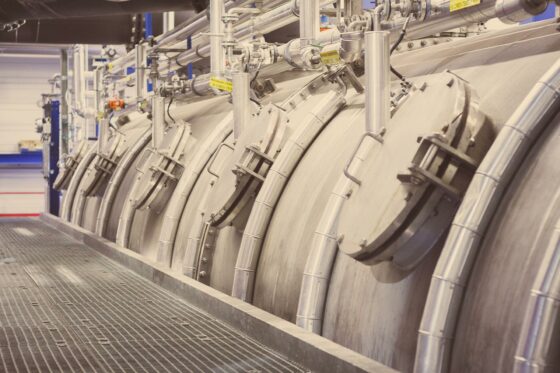
In the second part of the plant, the solution is further cooled by reducing pressure in a vacuum cooling crystallization plant, crossing the saturation line of sodium sulfate (Na₂SO₄).
Due to the low temperatures, Glauber’s salt crystallizes in the increasingly colder stages and is then separated from the solution.
The solution is then used to absorb some of the energy generated during the previous cooling by condensation and leaves the plant.
The resulting Glauber’s salt is then calcined in the third part of the plant.
Third Sub-plant: Calcination to Convert Glauber’s Salt (Na₂SO₄ 10H₂O) into Anhydrous Sodium Sulfate (Na₂SO₄)
In the calcination plant, anhydrous Na₂SO₄ is produced by melting the Glauber’s salt in its own crystal water and evaporating the water.
Initially, the salt is placed into a melting vessel.
The resulting water is removed in a forced circulation evaporator, typically configured as a single or multi-effect plant.
The resulting vapor can be used in other parts of the spinning bath preparation either as motive steam or heating steam.
The evaporated solution then flows back into the melting vessel and then goes with the calcined salt as a suspension to the salt separation unit.
After the anhydrous sodium sulfate has been freed from adhering solution, it is put into the dryer, where the sodium sulfate is dried to a residual moisture level that allows for trouble-free storage and transport.
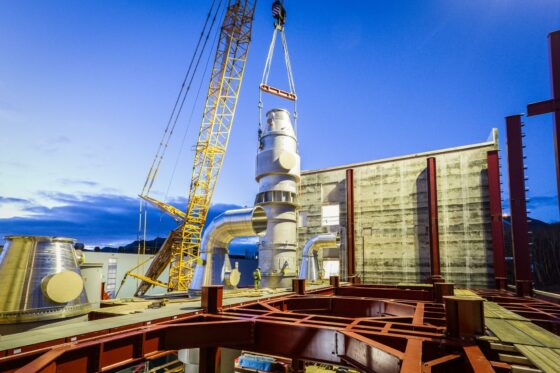
EBNER – your competent partner in plant engineering
Due to many years of experience in various industrial sectors and with various solutions, EBNER is your contact for optimally executing the process design, planning, delivery, and erection according to your needs.
Frequently Asked Questions
Why isn’t the spinning bath evaporated differently in the first step?
The evaporation of the spinning bath is typically carried out by flash evaporation as it creates the optimal balance of:
- Evaporation at low temperatures, thus minimizing corrosion behavior of the mostly acidic solution
- Utilization of waste heat generated in the overall process
- Achieving low specific steam consumption per kg of water evaporation
However, a trend towards evaporation plants with mechanical vapor recompression has developed in the past.
Why is the crystallization of Na₂SO₄ not carried out directly and Glauber’s salt crystallized first?
Due to the high accompanying components in the solution, the solubility characteristics are influenced.
Also, the resulting Na₂SO₄ would be produced in impure form.
What materials are used in spinning bath plants?
Due to the high corrosion potential of the solution due to contained sulfuric acid, especially evaporators and crystallizers as well as mixed condensers made of rubber-lined steel are used in the first two sub-plants.
The heat exchangers used are typically equipped with carbon tubes.
In the calcination plant, stainless steels can be used due to the low acid concentration.
Other applications

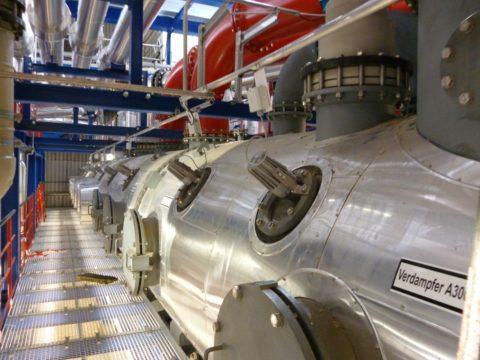
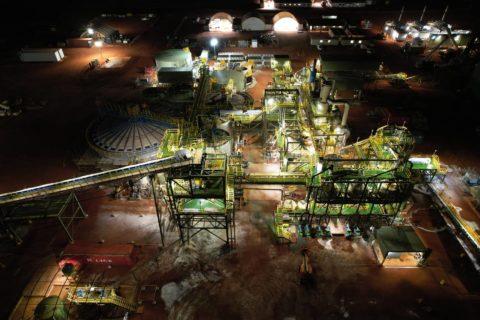
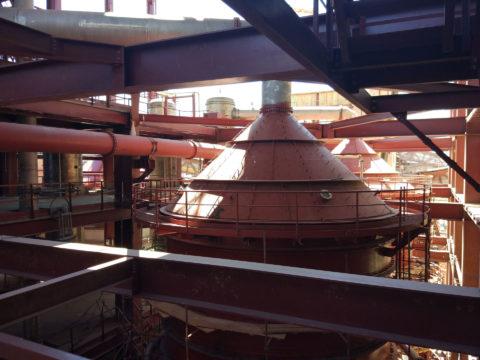
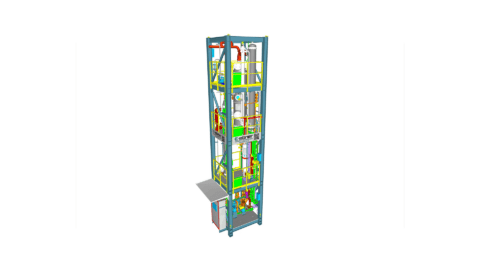
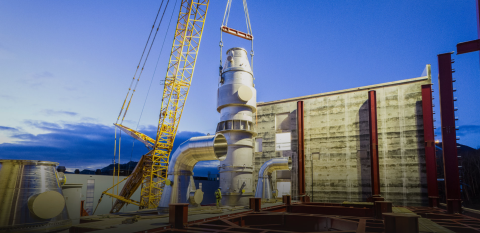
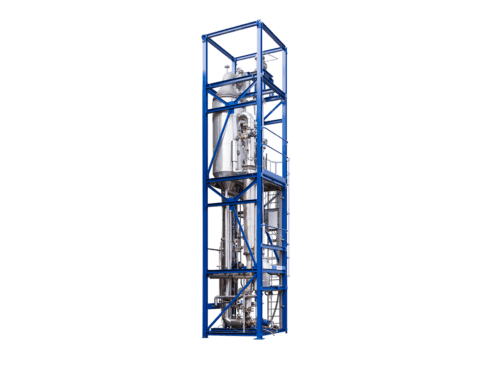
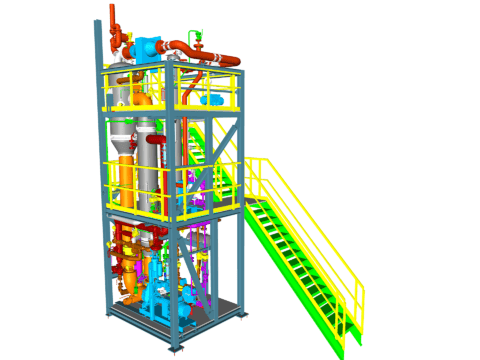
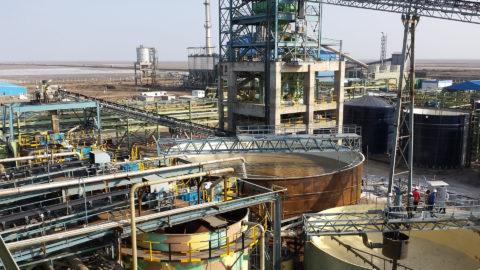
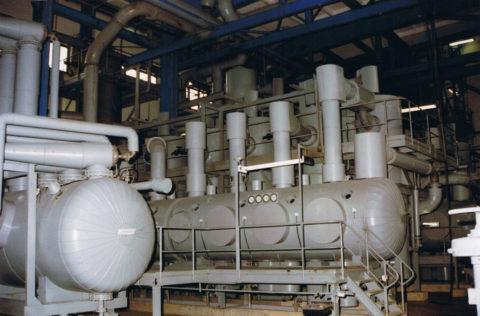
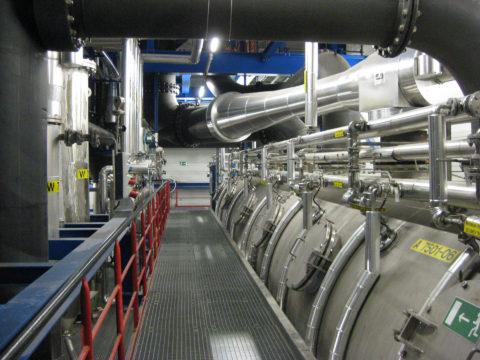
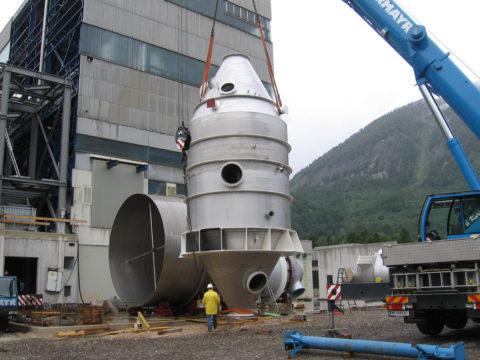
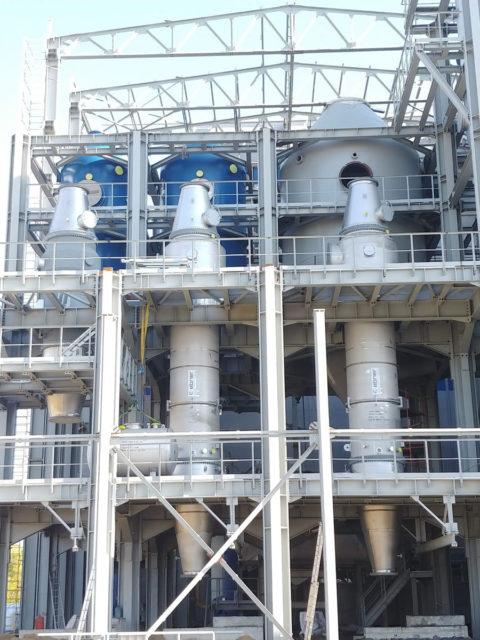
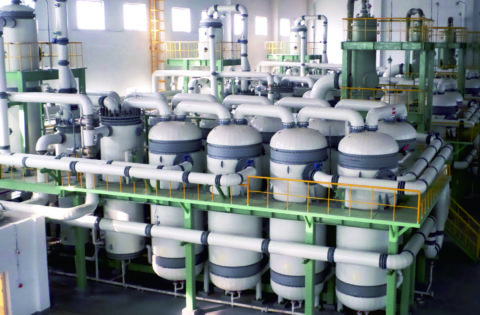
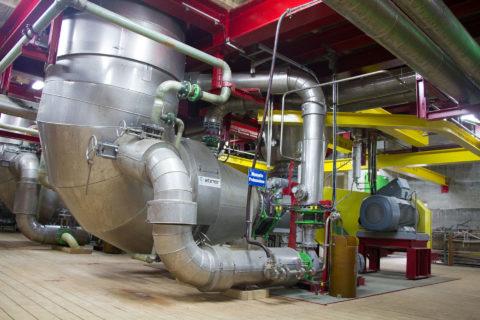