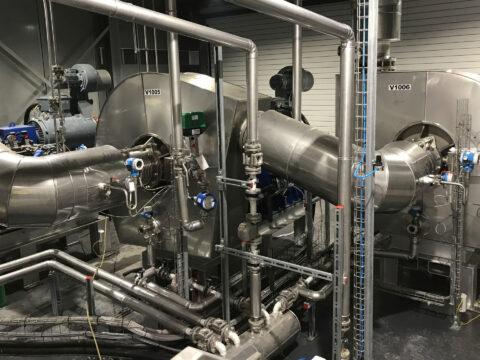
Degasssing Plants
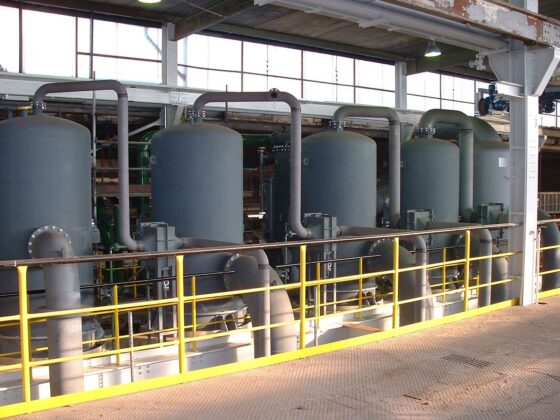
Operation and Process of Degassing
In single-stage vacuum degassing, the solution is sprayed in a vacuum container, referred to as EG1, where air and other gases are largely expelled. If necessary, a second stage, EG2, can be added, where gases are further removed by evaporating water from the solution. The resulting water vapor acts as a carrier gas and enhances degassing, allowing for optimal results. The expelled gases are extracted using steam jet devices ED1 and ED2. The water vapor is condensed in surface condensers OK1 and OK2 before the gases are compressed to atmospheric pressure by a vacuum pump VP.
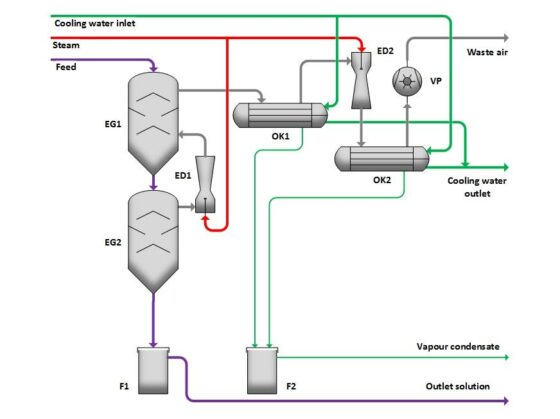
Degassing Principle
Degassing is an essential process where the partial pressure of gases dissolved in liquids is reduced by lowering the pressure, allowing these gases to escape. This principle is particularly relevant when air and other gases need to be removed from solutions to ensure the quality and purity of the liquid and to prevent unwanted outgassing in later processes.
Advantages of the Process
- Efficient Degassing: Fast and thorough removal of gases from liquids.
- Energy-Efficient Vacuum Generation: Minimized energy consumption during the process.
- Versatile Applicability: Suitable for various industrial applications and liquids.
Variants of Degassing Systems
- Condensation of the vapors in mixing condensers
- Condensation of the vapors in surface condensers
Frequently Asked Questions
What is the main purpose of degassing?
The main purpose of degassing is to remove dissolved gases from liquids to improve the purity and quality of the solution.
Why is a vacuum pump important for degassing?
A vacuum pump is essential to create a vacuum, which reduces the partial pressure of the gases, thus enabling their release.
Other Processes
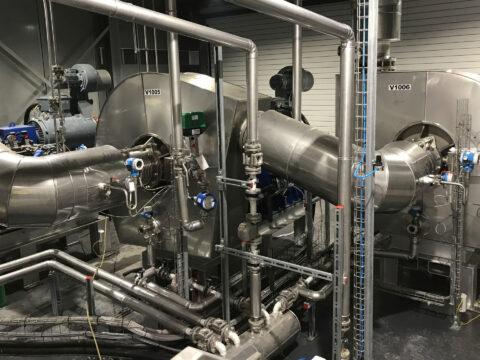
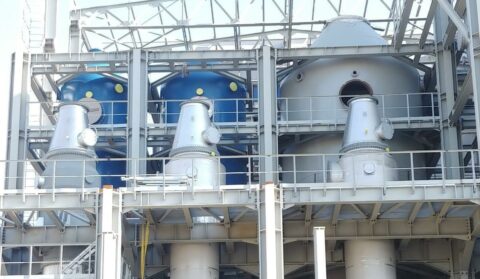
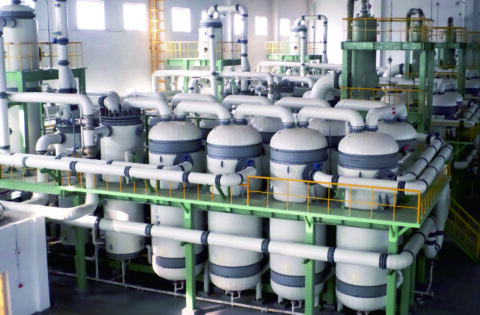
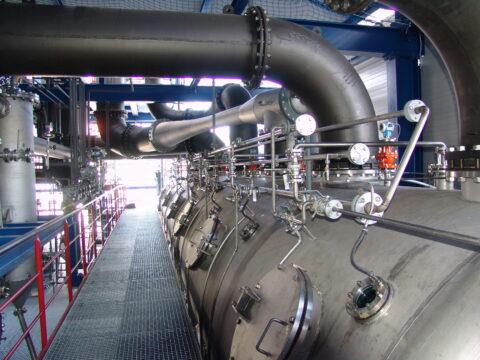
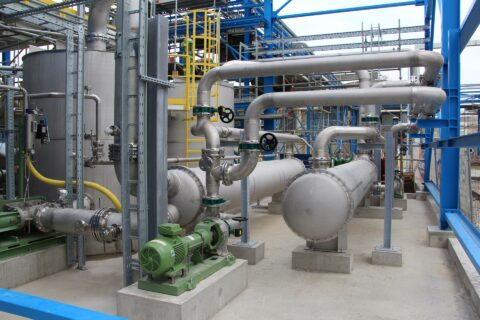
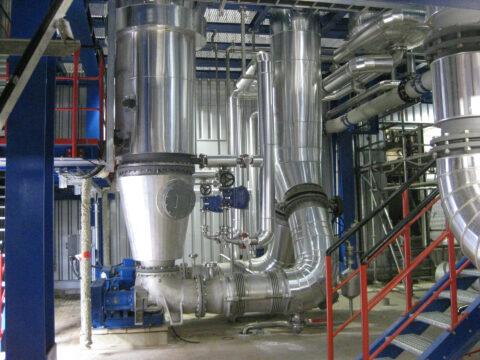
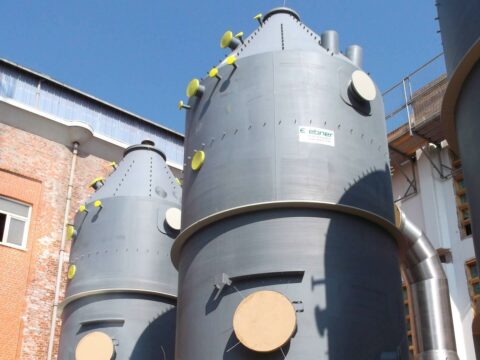
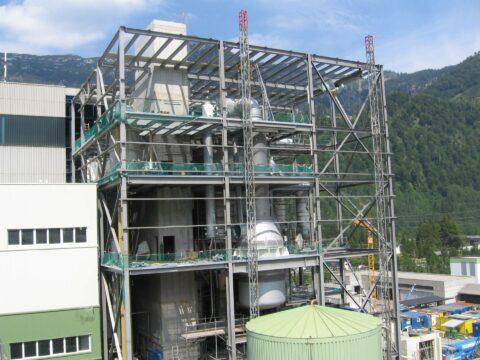
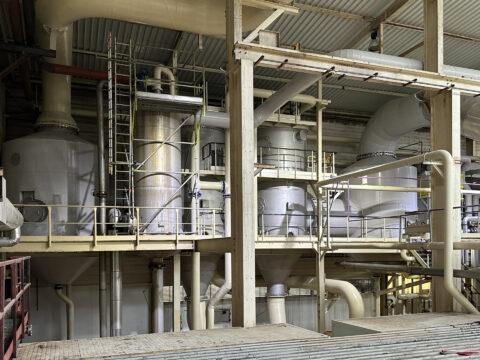