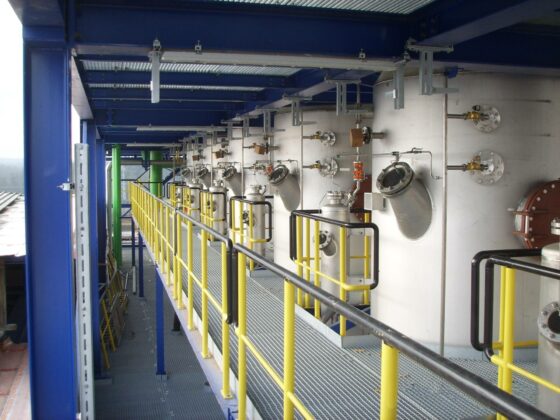
Crystallization Plants and Crystallizers
Crystallization is an essential process in various branches of industry that enables the targeted extraction of crystalline substances from solutions. At EBNER, we develop crystallization systems that are designed with precision and technological sophistication to create optimal conditions for crystal formation and recovery.
The crystallization of salts from solutions such as brines, process water or waste water is possible in a wide variety of ways. The choice is made primarily on the basis of the solubility of the salts contained. A distinction is made between two main variants:
- Evaporation crystallization, in which the saturation line of the salt to be crystallized is exceeded by evaporation of the solvent (usually water), resulting in crystallization
- cooling crystallization, in which the saturation line is exceeded by lowering the temperature of the solutions.
Depending on the general conditions, crystallization systems can be provided as:
- simple recirculating crystallizers with forced circulation or natural circulation
- as DTB (draft tube baffle) crystallizers and
- as horizontal crystallizers
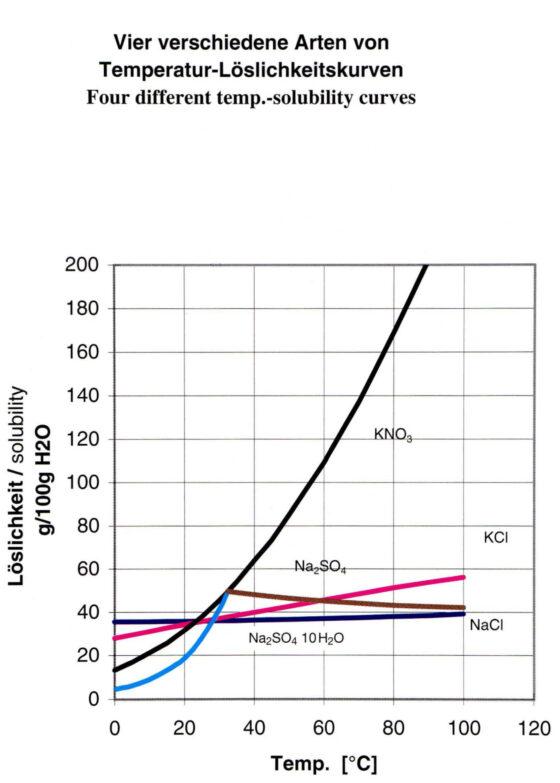
With a deep understanding of the thermodynamic and kinetic aspects of crystallization, EBNER develops systems that not only work efficiently and reliably, but are also tailored to the individual needs and requirements of your processes.
The following substances, among others, have already been crystallized in the past:
Substances crystallized by EBNER
Evaporation crystallization
In evaporation crystallization, similar to evaporation from solutions, the solvent (usually water) is evaporated by adding primary energy.
As described in the basic description of evaporation , there are various ways to crystallize salts:
- Single or multi-stage evaporation by supplying steam and condensing the vapor from the last stage using cooling water or cooling brine in mixing condensers or surface condensers
- Single-stage systems with mechanical vapor recompression, in which all of the vapor produced is used in the evaporator in order to be reused as heating steam after compression, or
- Single-stage systems with thermal vapor recompression, in which part of the vapor produced is compressed with live steam to ultimately be used as a heating medium. The non-compressed remainder of the resulting vapor is condensed at mixing condensers or surface condensers using cooling water or cooling brine.

In addition to the system scope of classic evaporation plants, salt separation is of course also necessary for evaporation crystallization – this usually consists of a pre-thickener (thickener or cyclone) and a mechanical separator (centrifuges, belt filters or similar are classically used here).
If required, this salt can then be dried in the next step (fluidized bed dryers or drum dryers are used here, for example).
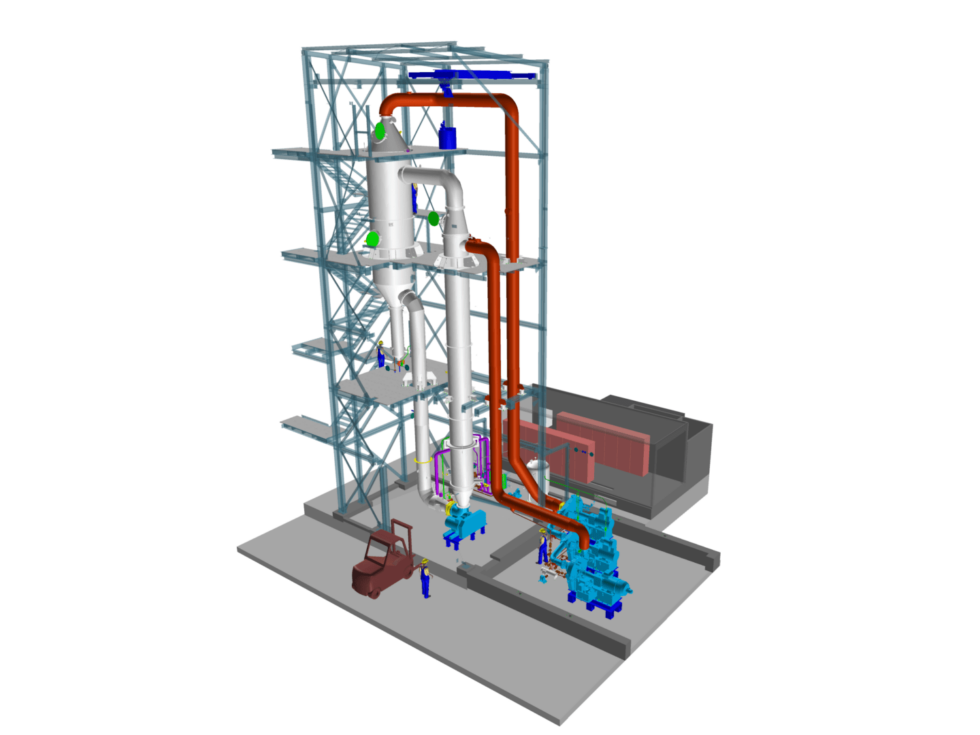
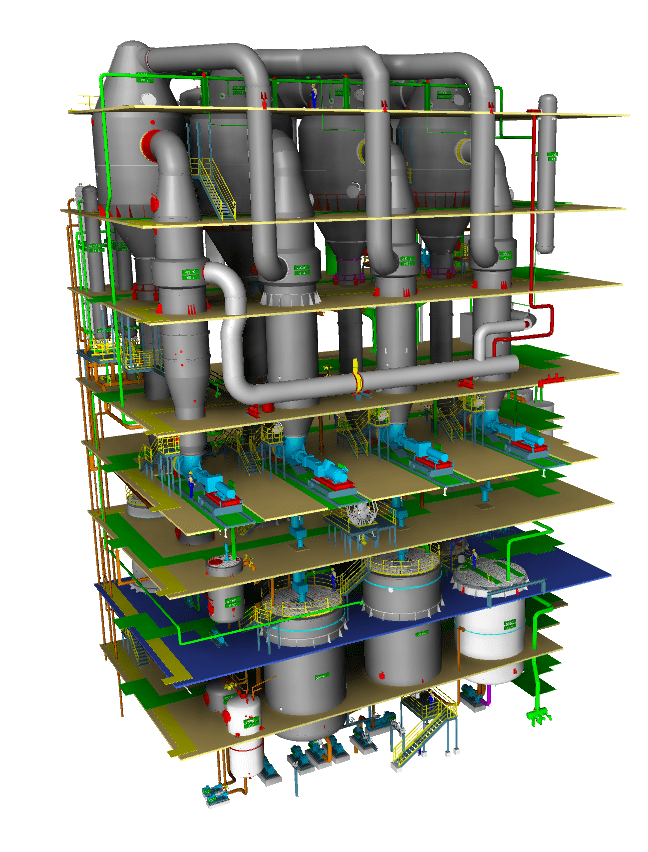
Areas of application for an evaporation crystallization system
- evaporation from sodium chloride solution and crystallization of sodium chloride (also called vacuum salt or common salt)
- the crystallization of anhydrous sodium sulphate
- the crystallization of ammonium sulphate
- the crystallization of lithium hydroxide or lithium hydroxide monohydrate
- the crystallization of lithium sulphate
- Crystallization of lithium chloride
- Crystallization of lithium carbonate
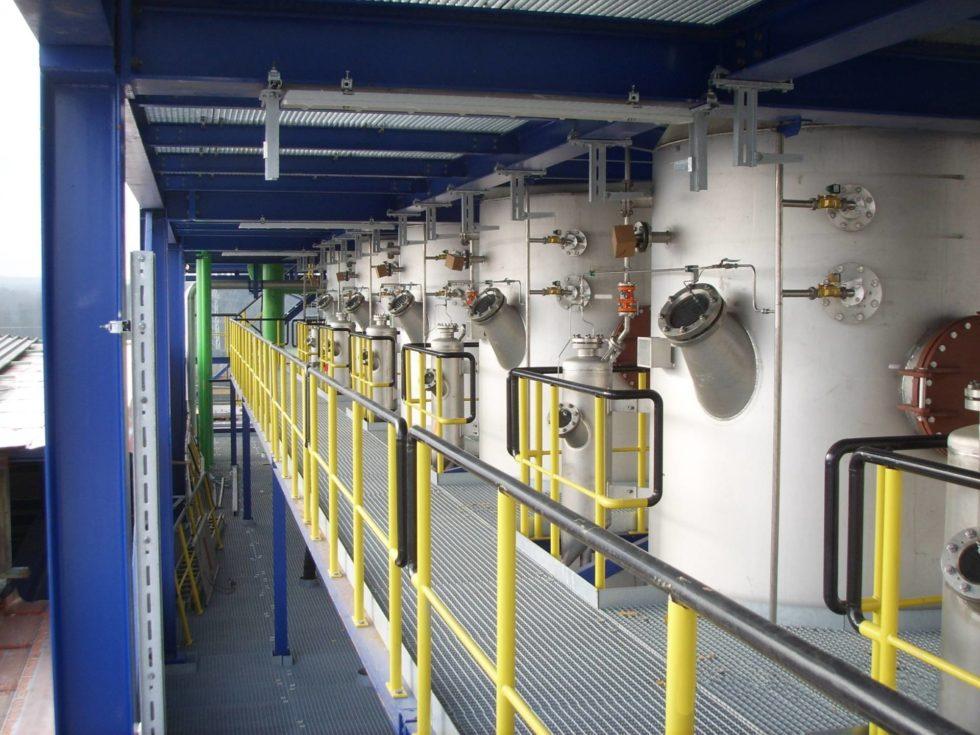
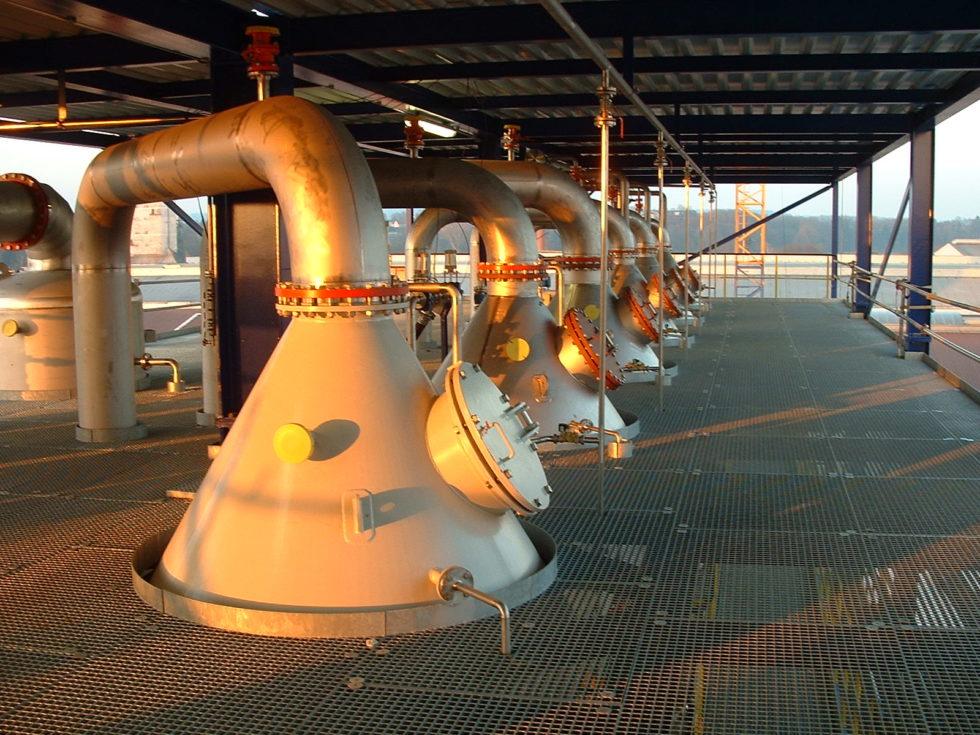
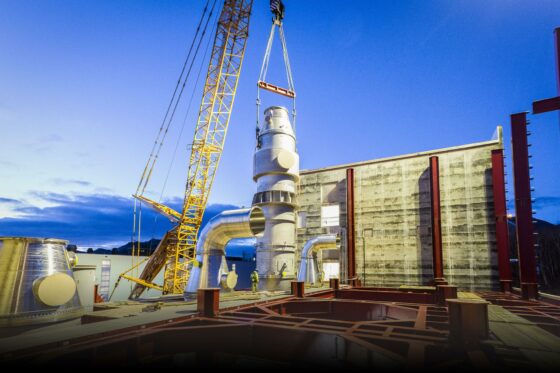
EBNER – your competent partner in plant engineering
Thanks to its many years of experience in a wide range of industries and with a wide range of solutions, EBNER is your contact partner for the optimum process design, planning, delivery and installation according to your requirements.
Frequently Asked Questions
At what temperatures is the evaporation crystallization system operated and how is the system designed?
Both the temperature and the circuit are determined on the basis of energy costs, individual thermodynamic process parameters of the solution and the corresponding solubility curves.
For example, it may be necessary for the hottest temperature in the solution circuit to remain below a certain limit in order to produce the desired salt – this is the case, for example, in the crystallization of lithium hydroxide monohydrate (LiOH H₂O) – if the conversion temperature is exceeded, the lithium hydroxide would precipitate as anhydrate (LiOH).
This phenomenon can ultimately be found with many sulphate salts (such as sodium sulphate – Na₂SO₄).
On the other hand, it is sometimes necessary not to fall below a certain temperature in order to enable good crystal growth due to a low viscosity of the solution – this is particularly important for salts that have to reach the necessary crystal sizes due to corresponding market requirements and are diffusion-limited by crystal growth.
What needs to be considered when designing an evaporation crystallization system?
In any case, evaporation crystallization plants are designed in such a way that a certain supersaturation is not exceeded during the corresponding evaporation of water (this depends on the salt to be produced) in order to prevent spontaneous nucleation.
This would only produce fine salt, which either has very high residual moisture levels during salt separation or cannot be separated using conventional centrifuges, for example.
In addition, the need for a minimum crystal size in accordance with market requirements would not be achieved.
On the other hand, a certain supersaturation must not be undercut – if the supersaturation is too low, the crystals present in the circuit will grow too slowly and will not reach a sufficient grain size.
Cooling crystallization
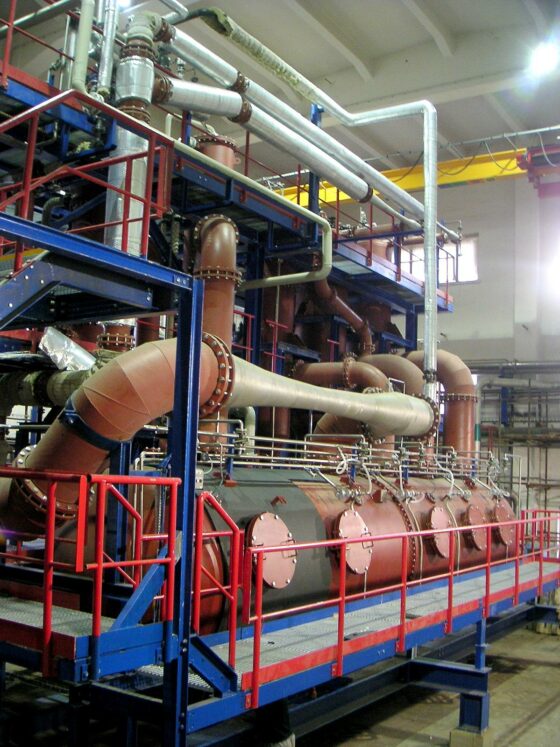
In cooling crystallization of the solution, crystallization of the salt is achieved by cooling the solution and bringing it below the saturation limit of the corresponding salt.
The process mainly used in industrial practice is vacuum cooling crystallization. In the vacuum cooling crystallization plant, evaporation is brought about by gradually lowering the pressure. This cools the solution and the salt precipitates by exceeding the saturation line. The cooling of the solution then results in the crystallization of the resulting salt.
This is then separated by an appropriate separation device, as described above on the subject of evaporation-crystallization.
Areas of application for a cooling crystallization plant
- Vacuum cooling crystallization of potassium chloride in fertilizer quality
- Vacuum cooling crystallization of potassium sulphate
- Vacuum cooling crystallization of magnesium sulphate heptahydrate
- Vacuum cooling crystallization of iron sulphate heptahydrate (FeSO₄ 7H₂O – also known as green salt)
- the vacuum coolina2ng crystallization of Glauber’s salt (Na₂SO₄ 10H₂O)
- the vacuum cooling crystallization of sodium carbonate heptahydrate (Na₂CO₃ 10H₂O)
- the treatment of industrial waste water
Another option for cooling crystallization is to cool the solution on surfaces – this is usually carried out using shell and tube heat exchangers.
This variant is mainly used to crystallize salts in small plant capacities at low investment costs, whereby this process can be used both discontinuously and continuously. Surface cooling is also used for cooling down to low temperatures.
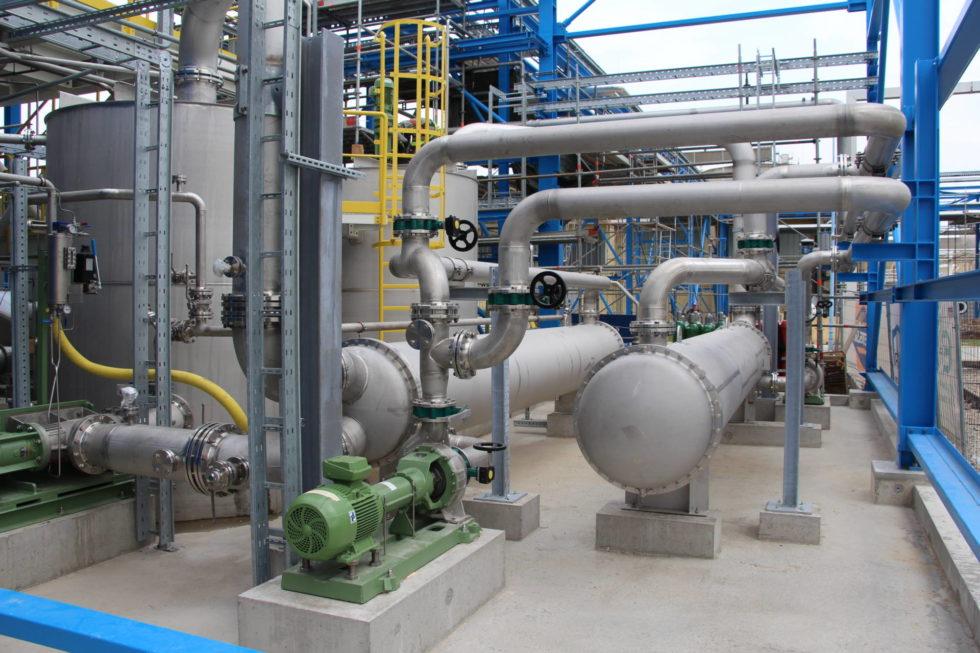
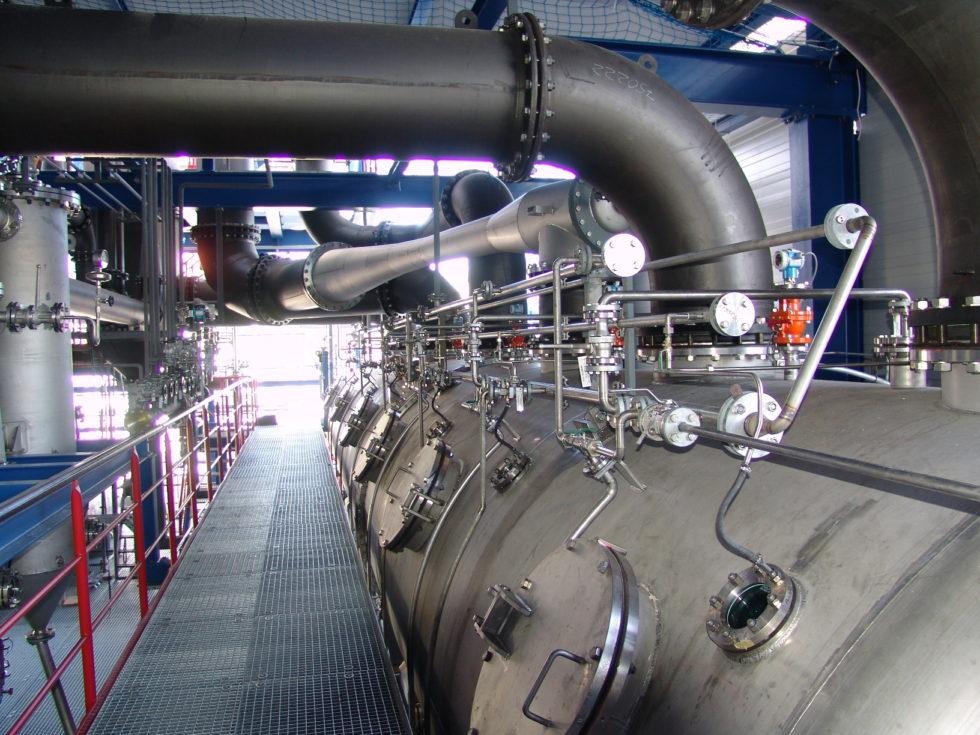
Thanks to decades of experience in crystallization technology and broad-based know-how, EBNER is your contact partner for the optimum process design according to your requirements.
Frequently Asked Questions
Why is the vacuum cooling process used more often than the direct cooling process?
The advantage of vacuum cooling crystallization is that cooling does not take place on surfaces which, due to the nature of the salt to be treated, namely the reduction in solubility as the temperature falls, leads to incrustation or blocking after a certain time and thus increased rinsing requirements.
Up to what temperatures can vacuum cooling crystallization be used?
Theoretically, it is possible to cool the solution to just before the freezing point. In practice, however, it must also be ensured that the resulting vapor can be condensed.
To do this, it must typically be condensed using surface condensers or directly in a cooling medium.
In some cases, compression, typically in Venturi steam ejectors, may be necessary.
Alternatively, the cold vapor can also be condensed in solutions with a high boiling point increase or vapor pressure decrease, such as concentrated lye or acid.
Why are shell-and-tube bundle heat exchangers mainly used for crystallization by surface cooling?
As incrustations are likely to form on the cooling surfaces of the system due to the decreasing solubility as the temperature falls, shell-and-tube bundle heat exchangers are primarily used. These offer the advantage of easy cleaning.
What needs to be considered for systems for cooling crystallization by surface cooling?
When designing the corresponding systems, it is important that the framework conditions are selected in such a way that incrustation on the cold surfaces is either prevented by a self-cleaning effect of the suspension or long service lives between two cleaning processes are ensured by sufficient surface reserves of the coolers.