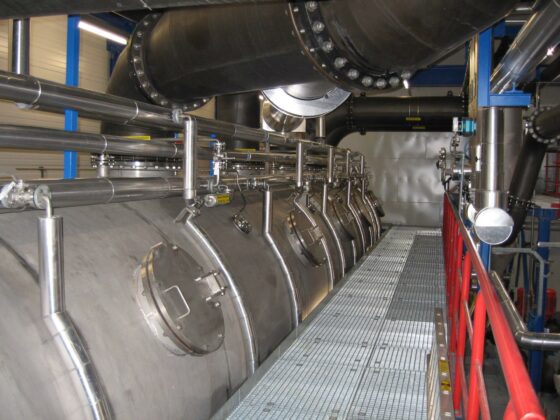
Evaporation Plants and Vaporization Plants
Evaporation and vaporization systems are essential technologies in various industrial sectors that specialize in the concentration of solutions and the recovery of solvents. These systems optimize processes through precise substance concentration and efficient solvent recovery, and are used in various application areas.
In industrial practice, evaporation plants are mainly used in the concentration of process solutions, the concentration of waste water or as intermediate steps in crystallization plants.
As a solvent (usually water) is to be extracted in the evaporation systems discussed here, heat must be added to the process in order to supply the energy required to evaporate the water.
Evaporation plants are usually designed as:
- Single or multi-stage plants with live steam heating
- Plants with mechanical vapor recompression
- Plants with thermal vapor recompression
- Plants with flash evaporation
- Plants for evaporation with falling film apparatus
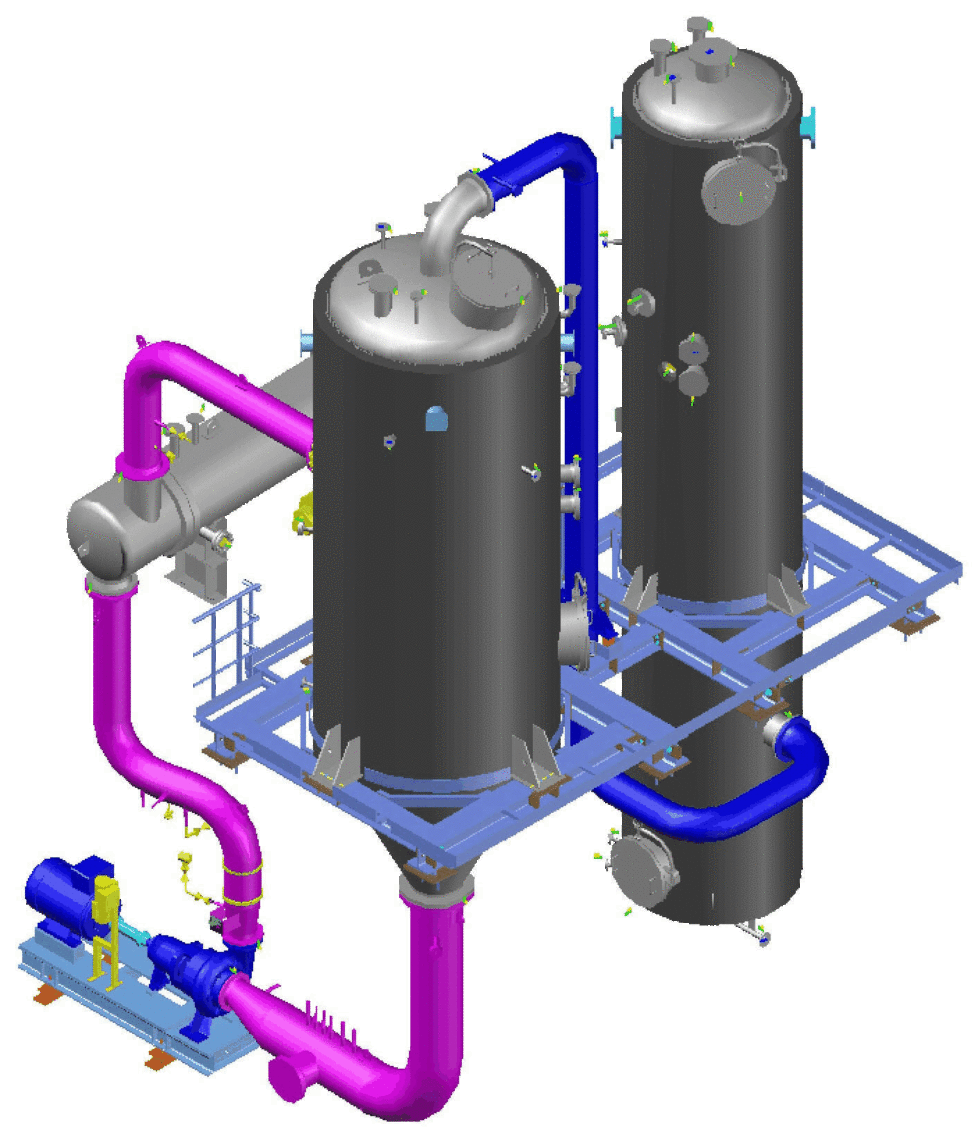
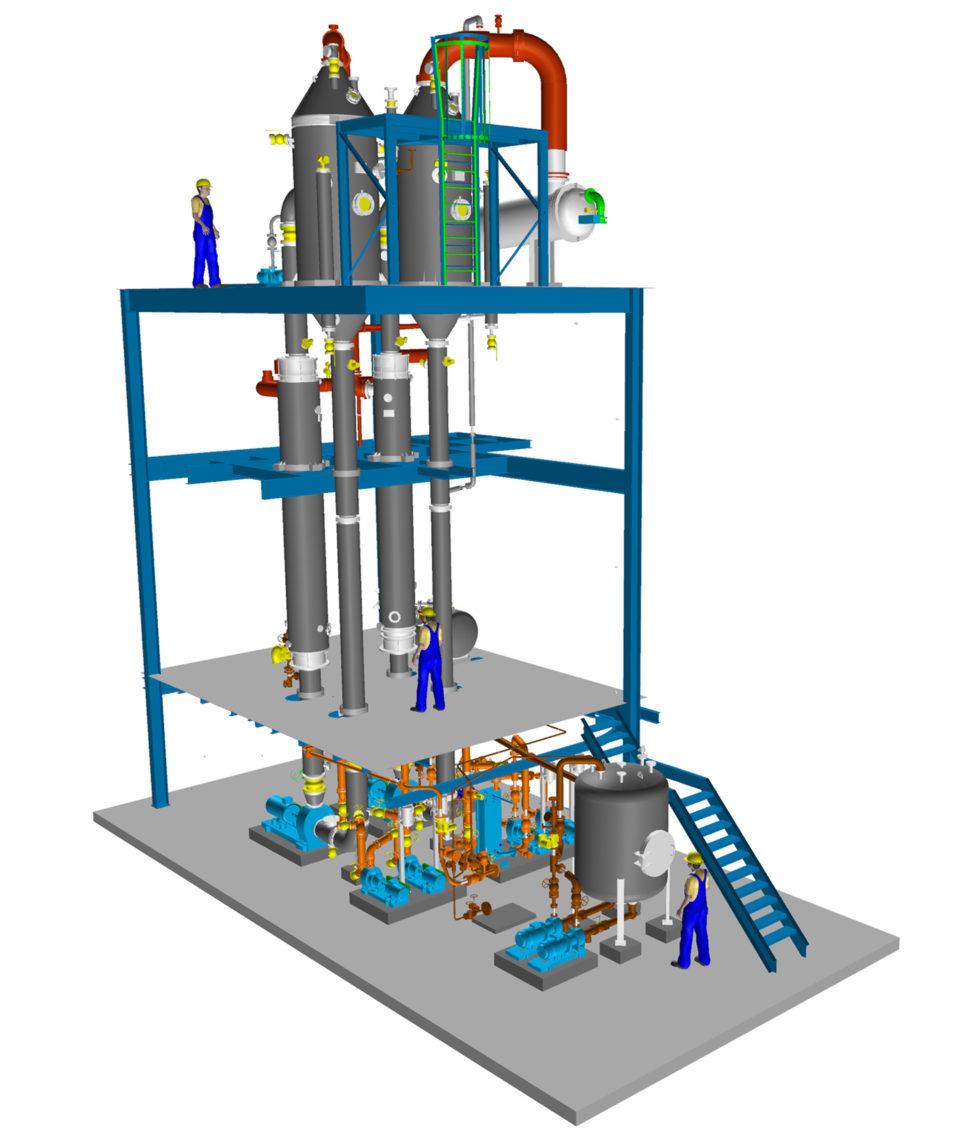
In all the applications described above, with the exception of flash evaporation, it is possible to use the systems
- as a classic forced circulation system with evaporator
- circulation pipe, circulation pump and heater element
- as natural circulation
- as a falling film evaporator
design.
Finally, the entirety of the requirements must always be considered.
If, for example, it is assumed that salts are likely to be partially lost in the process, the process with a classic circulation circuit is preferable, as falling film evaporators tend to become encrusted in the pipes, especially with different operating modes and due to the breakage of the liquid film.
The reason for this is that evaporation does not take place in the evaporation body as in the classic circulation circuit, but in the tubes of the falling film evaporator. This leads to the supersaturation of the corresponding ingredients being broken down at this point, resulting in incrustations.
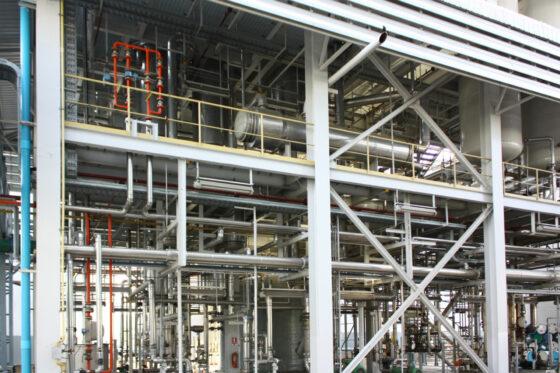
Evaporation and vaporization plants from EBNER: Tailor-made technology for concentration and solvent recovery
Discover a world of precise substance concentration and solvent recovery defined by technological excellence and customized solutions with EBNER’s evaporation and vaporization systems. Our experts are ready to work with you to develop the optimum solution for your requirements.
Media vaporized by EBNER:
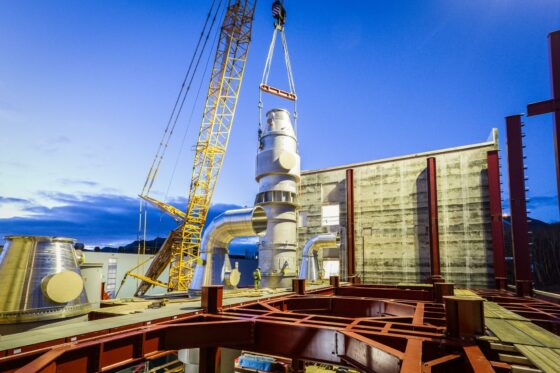
EBNER – your competent partner in plant engineering
Thanks to its many years of experience in a wide range of industries and with a wide variety of solutions, EBNER is your contact partner for the optimum process design, planning, delivery and installation according to your requirements.
Frequently asked questions
How is the number of stages selected for multi-stage systems with live steam heating?
In general, small numbers of stages mean low investment costs but high operating costs.
The maximum number of stages depends on the thermodynamic properties of the solution to be evaporated. If, for example, the boiling point increase (vapor pressure decrease) of the solution is very high, as is the case with systems with high calcium chloride (CaCl₂) or magnesium chloride (MgCl₂) contents, only a small number of stages can be selected, as otherwise the necessary temperature gradient between the first and last stage of the system would be too high or the necessary heat transfer surface, which is determined by the available temperature difference, would be very large.
What is the maximum number of stages in an evaporation system?
For evaporation systems with upright individual stages, it is common to have up to 6 stages.
It is also possible to select a higher number of stages in order to further reduce the final energy consumption of the live steam or cooling water consumption – this is then carried out with flash evaporation systems, which are common in the viscose fiber industry for evaporating spinning baths, for example.
What options are there for vapor compression and which procedure is used when?
In general, the resulting vapor can be
- completely compressed with mechanical vapor recompression
- partially compressed with thermal vapor recompression
Mechanical vapor recompression is used for solutions with low boiling point increases up to approx. 20K if no cooling water or live steam is available or if the costs for electrical energy are low compared to the costs for steam. The lower CO2 footprint should also play a role here.
If the investment costs of the system are to be low and it is unnecessary to be able to regulate the capacity of the system continuously, systems with thermal vapor recompression can be used.
What are the features of systems with mechanical vapor recompression?
In systems with mechanical vapor recompression, all of the vapor produced is compressed by a mechanical vapor compressor (single-stage or multi-stage fan or turbo compressor) and precipitated on the heating element of the system. This makes it possible to use the condensation enthalpy of the vapor vapor to provide the energy required to evaporate the water from the solution.
The compressor therefore only has to perform the corresponding compression work, which is necessary to overcome both the increase in the boiling point (reduction in vapor pressure) of the solution and to generate the necessary temperature gradient to enable condensation of the vapor on the heat exchanger.
Depending on the ratio of evaporation volume to inlet volume, these systems are generally able to be operated without live steam in normal operation.
Since, as described, the vapor compressor must overcome the increase in boiling point (decrease in vapor pressure) of the solution, and the corresponding compressors are only able to achieve a certain increase in pressure, several compressors arranged in series are required depending on the application.
Since, in addition to the electrical energy consumption, the CAPEX also increases with a high boiling point increase (vapor pressure reduction), mechanical vapor recompression is only economical up to a certain boiling point increase of the solution.
In systems with mechanical vapor recompression, it is possible to continuously regulate the capacity of the system in the operating range.
What are the features of systems with thermal vapor recompression?
In systems with thermal vapor recompression, similar to mechanical vapor recompression, a part of the vapor produced during evaporation compressed by means of a venturi steam jet apparatus and brought to a higher pressure level.
The mixture of live steam and vapor is then able to condense on the heater. As there is ultimately a surplus of energy in the entire system due to the balance, some of the resulting vapor must be condensed on a mixing condenser or surface condenser.
Due to the mixing of fresh, pure motive steam with vapor and thus contamination of the condensate, this evaporation technology has generally proved to be no longer economical in recent years.
Since a steam jet unit has a small capacity range, it is difficult to control the capacity. To regulate the capacity of the system, several steam jets can be installed, which can then be switched on or off individually. This allows the capacity to be regulated in stages.